Suspension spraying
Suspension spraying
FINEST LAYERS FOR PRECISE RESULTS
A completely new type of layer structure enables fascinating applications
SUSPENSION SPRAYING TECHNOLOGY
SUSPENSION SPRAYING TECHNOLOGY
PRECISION IN NANO DIMENSIONS
Suspension spraying is a decisive further development of thermal spraying. Whereas in conventional processes the coating material is processed in powder form, here we use a suspension, a mixture of finely dispersed particles, often in the nanometer or sub-micrometer range, dissolved in a liquid.
The advantages of suspension spraying are manifold. The applied layers are denser and therefore have a higher insulating capacity, improved thermal and electrical conductivity and high corrosion resistance.
By using nano- and submicrometer particles, coatings can be produced in such a way that they have a large nanostructured surface. This makes superhydrophobic properties possible. This is known as the lotus effect and is used for self-cleaning or anti-icing coatings.

YOUR ADVANTAGE
“Suspension spraying is a thermal spraying process that opens up completely new fields of application. Suspensions enable very thin coatings. Another revolution in coating technology to close the gap between classic thin-film technology and thicker coatings. Particularly interesting in the fields of power electronics, heat conductor layers and medical technology.”
Sven Hartmann
Managing Director / Dr.-Ing. M.A. MBA SFI
UNIQUE ADVANTAGES OF SUSPENSION SPRAYING:
- Nanostructured layers: The nanoparticles in the suspension enable the production of layers with a particularly fine microstructure, resulting in exceptional mechanical and functional properties.
- Flexibility in the choice of materials: The process allows a wide range of materials to be processed, including ceramic, metallic and even organic materials.
- Novel layer structures: The unique structure of the layers opens up new application possibilities, for example in sensor technology, biomedicine or high-temperature insulation.
Finest particles, maximum performance
In the suspension spraying process, the suspension is fed into a flame. This heats the starting material, melts it and accelerates it onto the substrate to be coated. This process produces an extremely fine and uniform coating. Suspensions enable the supply of nanostructured starting material. Its properties are transferred to the coating. The nano-properties give the applied coating special characteristics that cannot be achieved using traditional coating processes.
SUSPENSION SPRAYING TECHNOLOGY
SUSPENSION SPRAYING TECHNOLOGY
AREAS OF APPLICATION AND POTENTIAL
Suspension spraying is particularly suitable for high-tech applications where conventional spraying processes reach their limits. Typical areas of application include wear protection, superhydrophobic surfaces, electrodes with large surface areas, electronics, aerospace, medical technology and energy generation.
The ability to apply nanostructured layers makes suspension spraying a key technology for the development of functional surfaces with very specific properties.
Completely new layer structures can be realized, thus expanding the spectrum of surface finishing with fascinating and future-oriented applications.
Insulation layers
For power electronics, heat conductor layers and medical technology
- In a joint research project with the Institute of Materials Science at TU Dresden, HVOF and suspension-sprayed insulation layers are being developed.
- These layers are denser than conventionally thermally sprayed layers and therefore have a higher insulating capacity with a lower layer thickness.
- Due to their high thermal conductivity, they are to be used in circuit carriers for power electronics, which are increasingly being used in cars and hybrid vehicles in particular.
- Project sponsor: BMWi, Central Innovation Program for SMEs ZIM; funding code: KF3197501
Other areas of application for dense, suspension-sprayed insulation layers include
- Heat conductor layers for hobs, plastic injection molding and many other areas
- Medically approved, sealant-free insulation layers
DEMONSTRATOR: CIRCUIT CARRIER WITH CONDUCTOR TRACKS
CROSS-SECTION OF A DENSE CERAMIC LAYER
SOURCE: F.-L. Toma, A. Potthoff, L.-M. Berger, C. Leyens: “Demands, Potentials, and Economic Aspects of Thermal Spraying with Suspensions: A Critical Review” in Journal of Thermal Spray Technology, Vol 24(7), 2015, S. 1143–1152
CROSS-SECTION THROUGH MULTILAYER HEATING SYSTEM
SOURCE: IFKB Uni Stuttgart
Thin precious metal layers
For switching contacts and heating conductor layers
- TherMeS research project, together with the Institute for Production Technology of Ceramic Components at the University of Stuttgart
- Project sponsor: BMWi, Central Innovation Program for SMEs ZIM; funding code: KF3197502AG4
- Suspension-sprayed metal coatings
Areas of application
- Silver alloys and silver dispersion layers (e.g. silver-graphite, silver-tin oxide) for switching contacts, e.g. in fuse boxes and relays
- Heating conductor layers made of thin (10 µm to 50 µm) nickel-chromium alloys
Further applications
- Heating conductor layers made of thin (10 µm to 50 µm) nickel-chromium alloys
Wear protection
- Suspension-sprayed chromium oxide layers are an environmentally friendly and longer-lasting hard chrome replacement
- Due to their nanostructure, crack propagation is suppressed and hardness is increased compared to conventional chromium oxide layers
- The illustration shows that in conventionally sprayed chromium oxide layers, crack growth occurs parallel to the layer layers, while the cracks in a suspension-sprayed chromium oxide layer propagate evenly in all directions. In addition, the cracks in the supension-sprayed layer spread less strongly overall. This increases the wear resistance.
AREA OF APPLICATION: WEAR PROTECTION COATING FOR PISTON RODS
SOURCE: A. Killinger, A. Rempp, P. Müller, A. Manzat und R. Gadow, Hochgeschwindigkeitsflammspritzen mit Suspensionen aus nano- und submikronskaligen Oxidpulvern High-velocity oxy-fuel spraying with suspensions consisting of nanoscale and submicronscale oxide powders in: Thermal Spray Bulletin to be published in 2015 Hrsg. GTS eV
VIEW OF NANOSTRUCTURED SURFACE
SOURCE: A. Killinger, Suspensionsflammspritzen – Thermokinetisches Beschichtungsverfahren zur Verarbeitung submikron- und nanoskaliger Werkstoffe In: Stuttgarter Impulse – Fertigungstechnik für die Zukunft Schriftliche Fassung der Vorträge zum Fertigungstechnischen Kolloquium am 29. bis 30. September 2010 in Stuttgart; FTK 2010 Stuttgart, 2010, ISBN: 978-3-925589-51-5
Superhydrophobic surfaces
-
Suspension-sprayed coatings can be produced in such a way that they have a large, nanostructured surface (see image “Top view of nanostructured surface”).
- This makes superhydrophobic properties possible.
Superhydrophobic surfaces are also known as the lotus effect. They are used for
- Self-cleaning coatings
- Anti-icing coatings (e.g. for airplanes or wind turbines)
Electrodes with a large surface area
The large, nanostructured surface of suspension-sprayed coatings can also be used for more effective electrode processes, such as
- Electrolysis
- Electrocatalysis
Fuel cells are a typical application example
VIEW OF NANOSTRUCTURED SURFACE
SOURCE: A. Killinger,
Suspensionsflammspritzen – Thermokinetisches Beschichtungsverfahren zur Verarbeitung submikron- und nanoskaliger Werkstoffe
In: Stuttgarter Impulse – Fertigungstechnik für die Zukunft
Schriftliche Fassung der Vorträge zum Fertigungstechnischen Kolloquium am 29. bis 30. September 2010 in Stuttgart; FTK 2010
Stuttgart, 2010, ISBN: 978-3-925589-51-5
CROSS-SECTION OF A THERMAL BARRIER COATING: HIGH POROSITY
SOURCE: A. Killinger,P. Müller and R. Gadow, High Velocity Suspension Flame Spraying and Suspension Plasma Spraying of Oxide ceramics in: Thermal Spray 2012: Proceedings of the International Thermal Spray Conference (May 21-24, 2012, Houston, Texas, USA), Eds: Basil R. Marple, Arvind Agarwal, Margaret M. Hyland, Yuk-Chiu Lau, Chang-Jiu Li, Rogerio S. Lima, and André McDonald, ASM International, 2012
Side view of a thermal insulation layer: columnar growth
SOURCE: Forschungszentrum Jülich, N. Schlegel
Thermal barrier coatings
Suspension spraying achieves a layer growth that was previously only possible with expensive vacuum techniques:
- With a suitable choice of coating parameters, columnar-growing and porous coatings can be produced.
- Such coatings are used as thermal barrier coatings in gas turbines and aircraft turbines.
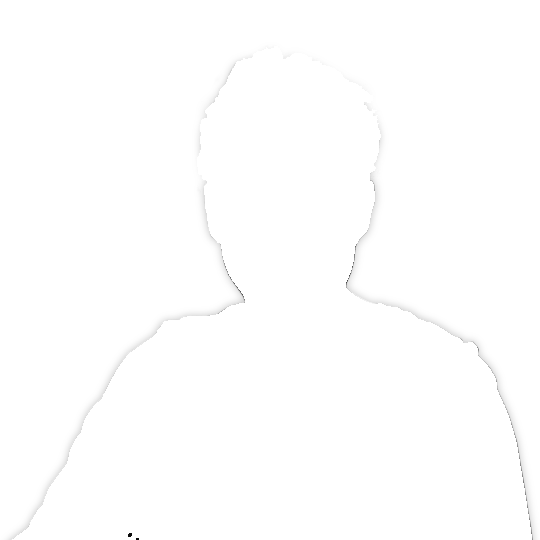
Your contact person
Chakib Lefkir
Application Development / B.Eng.
Your contact person
Chakib Lefkir
Application Development / B.Eng.
SPRAYING PROCESS
SPRAYING PROCESS
MORE ABOUT OUR INNOVATIVE PROCESSES
Find out more about our unique spraying processes and their applications. From cold gas spraying and thermal spraying to suspension spraying – we can help you find the right solution for your project.
RESULTS
RESULTS
IMPRESSIVE RESULTS
Discover the innovative applications and fascinating results of suspension spraying. This advanced process enables exceptionally dense and uniform coatings that meet the highest standards.
Complete production
Complete production
MAXIMUM EFFICIENCY THROUGHOUT THE ENTIRE PROCESS
Our complete production combines various manufacturing processes and offers tailor-made solutions for complex requirements. This approach ensures that products are manufactured faster, more efficiently and with outstanding quality.